Author |
Message |
AJ Quick Samba Member
Joined: July 20, 2006 Posts: 539 Location: Minnetonka, MN
|
Posted: Thu May 08, 2008 12:14 pm Post subject: |
|
|
substock wrote: |
I got one that does an honest 7CFM with 110, It sucks over 20 amps from the wall so you need a 30 amp circuit to run it....it'll also accept a conversion to 220 |
Wouldn't something like that defeat the purpose?
I would assume if you have to put in a 30 amp circuit.. you should make it a 30 amp 220 circuit. _________________ Read My Beetle Restoration Blog!
http://www.RideSpace.net/
http://www.AJQuick.com/ |
|
Back to top |
|
 |
substock Samba Member

Joined: October 14, 2007 Posts: 69 Location: MC, IA
|
Posted: Thu May 08, 2008 7:41 pm Post subject: |
|
|
Quote: |
Wouldn't something like that defeat the purpose?
I would assume if you have to put in a 30 amp circuit.. you should make it a 30 amp 220 circuit. |
pretty much... I got it because it would run on 110v. I couldn't get 220v easily or cheaply to my garage at the time, but I had a 30amp breaker dedicated to the garage outlets, so it was the biggest compressor that I could get that could run on 110v that was available to me. I know many garages have just a small 15A lighting circuit, so this compressor wouldn't do....it was just the biggest unit that I could find that used 110v service. If I wired the compressor for 220v it would run easily on a 220v 15A circuit...but it wouldn't perform any better.
I got a new garage now with 220v 200A service....and 4 VW's awaiting restoration. I'm still hunting for a better compressor. |
|
Back to top |
|
 |
zxylon Samba Member
Joined: January 30, 2006 Posts: 117 Location: WA
|
Posted: Sat May 17, 2008 10:35 am Post subject: |
|
|
I'm about to get two 80 gal compressors that run on 220 at about 13 cfm @ 90 psi from my friends dad. They're only 6 months old but they get used hard. 4 nail gun working off of one form about 16 hrs a day 5 or 6 days a week. He said they switch out air compressors every 6 months and thinks that the regulator or the seals might just go out (probably cause of the dusty environment). I was wondering a few things. How hard is it to do a tune up on an air compressor like that and how should I wire it up if my breaker box is already full? Should I just run straight power to a new box just for the compressor? I was going to put it on the oppisite side of the garage with a inline on/off throw switch and just put a breaker just before it. maybe add in an outlet and a light on that wall from the new box over there too. Not sure, it's been a while since I've done electrical (about 5 years since my dads machine shop) so I'm not sure what would be the best bet. |
|
Back to top |
|
 |
Campy Samba Member
Joined: January 10, 2005 Posts: 4933 Location: Chico, CA
|
Posted: Fri May 23, 2008 9:09 pm Post subject: |
|
|
A number of years ago, I replaced my 110 volt mig welder with a new 220 volt Millermatic. There was no 220 volt outlet in my garage and my breaker panel was full up, with no space for another trip switch. What I did was buy a dual trip switch (110 volt switch on the inside and a 220 volt switch on the outer side) and replace the one in the bottom hole with it. The 220 volt electrical outlet box went on the inside of the wall, connecting straight through the wall to the backside of the breaker panel on the outside of the wall.
When I got my used 220 volt dual stage upright air compressor, I mounted it on rubber pads on the cement floor near the electrical outlet, mounted the magnetic starter and electrical power box side-by-side on the wall, and ran the wires through the flexible tube from the electrical power box to the side of the electrical outlet box to the electrical outlet. _________________ Don't worry; be happy. (Baba) |
|
Back to top |
|
 |
zxylon Samba Member
Joined: January 30, 2006 Posts: 117 Location: WA
|
Posted: Sat May 24, 2008 6:39 am Post subject: |
|
|
I just got 2 80gal 2 stage belt driven Husky Pro air compressors from a friends dad. They are Campbell Hausfeld certified compressors (at least that's what the info plate on them says). They were used only 6 months in a framing warhouse so they're dusty as hell and supposedly something is not working with them. How much of a pain in the ass is it to do a rebuild/tune up on them to get 'em going again? I'm gonna sell one 80gal and keep one and he's supposed to be bringing up another 60 gal for me too. Just one big step towards my media blast/paint booth!
Another thing too. I need to wire it up to my breaker but there's no more room in the box. I was thinking about running wire over to another box nearer to the compressor and having a throw switch on it too. Possibly use that other box for another outlet and light right there and maybe run power from it out to my booth so I can have a light or two in it and maybe an outlet for heat so I can get some good paint finishes in there. How should I go about doing that? Thanks! |
|
Back to top |
|
 |
AJ Quick Samba Member
Joined: July 20, 2006 Posts: 539 Location: Minnetonka, MN
|
Posted: Sat May 24, 2008 11:43 am Post subject: |
|
|
For the compressor rebuild.. it is no different from rebuilding an engine. You should have a parts manual that lists torques and part numbers for replacement numbers.
For the electrical.. hire an electrician. No one else can really help you.. don't mess around with electricity if you don't know what you are doing. _________________ Read My Beetle Restoration Blog!
http://www.RideSpace.net/
http://www.AJQuick.com/ |
|
Back to top |
|
 |
zxylon Samba Member
Joined: January 30, 2006 Posts: 117 Location: WA
|
Posted: Sat May 24, 2008 12:14 pm Post subject: |
|
|
I've wired up my dads shop twice (he's had two different machine shops so far due to expansion) and it was never a problem for me to wire up industrial machines. I just wanted to see what would be suggested as a better setup. Either to just use a new breaker box with no throw switch or to have the throw switch for the compressor as well as a breaker and then have breakers for the other electrical components? |
|
Back to top |
|
 |
AJ Quick Samba Member
Joined: July 20, 2006 Posts: 539 Location: Minnetonka, MN
|
|
Back to top |
|
 |
campacker Samba Member
Joined: June 09, 2008 Posts: 35 Location: Upstate Ny
|
Posted: Sat Aug 02, 2008 8:57 pm Post subject: |
|
|
Just as an indication on how big they are and the capacity. I recently bought a 30 gal 3 hp kit form homedepot for like $249.00 sounded like a great because it had an impact wrench, diegrinder, spray gun, impact hammer, tire inflater and I think one or two other things. here is the fun part I bought a farm hand cutoff tool at tractor supply (the instore brand)and tried to cut through a stud with a 13mm nut on it and I had to stop 3 -4 times to get the job done. I tried to use a manual tool to get the screw on the doors off and then swaped to the impact wrench and had to stop once to let the compressor catch up on the last 2 screws.
If doing any painting go with a big capacity tank so when the compressor kicks on you can time when it is time to get ready to stop you dont want to have the paint sputtering on your car. Go no smaller than a 30 gal.
As for tools you want a compressor that has a high capactiy on it to keep up with your tools each pneumatic tool has the capacity it works best at. Make sure the compressor can keep up with it if not either get a smaller tool or bigger comp. Hope this helps. |
|
Back to top |
|
 |
william simpson Samba Member
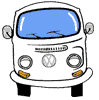
Joined: March 17, 2007 Posts: 41
|
Posted: Thu Sep 04, 2008 9:52 am Post subject: Compressor size? |
|
|
Depends what your doing,Commercial or home? Home the smallest smart buy is 33 gallon craftsman,it will perform most all your needs for the home do it your selfer with quality results weather it be an impact wrench or air spray gun.My 11 gallon 2 hp runs my impact wrench and yes I painted my bus with it too.......I do not recomend that for folks that dont have years of experiance.The craftsman 33 gallon is a good buy ,has warranty,a place you can take it back too with no problem,and its not a piece of junk,plus you can plug it into a wall socket with a 30 amp breaker.....Bigger 60-80 gallon single stage or 2 stage compressors are great if you are willing to spend hundreds to have it wired right or unless you are an electrician or have a freind that is one......For around $300 bucks a 33 gallon craftsman will get ya happy.......I have painted and done body work for over twenty five years and have compressors from 8 gallon to 120 gallon,One more time 33 gallon craftsman is what I would go with for home I want to do it all compressor.....CFM is key (cubic foot per minute) All tools require different cfm ,A 33 gallon will work all the small,medium and even some of the large tools,Leave sand blasting to your local sand blaster.With out experiance you can destroy what you want to make nicer or even kill yourself,Silicoses is deadly.They now use media blasting with keeps lungs and your loved ones happy........Happy bus driver , "WILL" |
|
Back to top |
|
 |
Campy Samba Member
Joined: January 10, 2005 Posts: 4933 Location: Chico, CA
|
Posted: Thu Sep 04, 2008 5:06 pm Post subject: |
|
|
If you can find an oil bath Craftsman air compressor with a belt drive, it would be alright. All of the air compressors that they have at Sears in Chico are oilless (plastic piston). Also, the direct drive ones are really noisy. If you will be using an air compressor a lot, do not buy an oilless one.
Before I picked up a nice DeVilbiss two stage air compressor with an 80 gallon tank for $400, I used a Campbell Hausfeld oil bath air compressor with a 27 gallon tank for eight years, and I thrashed the shit out of it, and it kept working good. The only thing with using a smaller air compressor was that when I used an air tool such as a disc cutter that uses a lot of air, I would have to wait for pressure to build back up in the tank more than I liked. _________________ Don't worry; be happy. (Baba) |
|
Back to top |
|
 |
reasley Samba Member
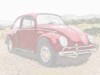
Joined: May 10, 2007 Posts: 170 Location: gone
|
Posted: Sat Sep 06, 2008 10:43 pm Post subject: |
|
|
There’s a lot good information here about compressors, but little to no info regarding air tools. The common scenario is you spend the bucks and buy a nice 10-12 cfm compressor, 1/2” impact gun and maybe a cutoff tool or a die grinder. Then you get it all hooked up and it does not perform to your expectations. Usually you blame the retailer for having sold you a crappy tool. Actually your can blame yourself for making an uninformed purchase decision.
The problem lies with the amount air actually needed to drive the tool to acceptable performance. Air tools must be matched to the available air flow to function properly. Much like the horsepower ratings on compressors, air tools manufacturers use cfm numbers that are not very helpful.
If you paid attention at all, that ½” impact wrench had specs that said it would produce up to maybe 350 foot pound of torque and had an average air consumption of 8 cfm. So you figured your 10 cfm compressor would more than handle this tool. Well you probably figured wrong. The 350 ft lbs is achieved at full load and full load is going to be closer to 22 cfm. With a 60 gallon tank you can potentially put out 22 cfm for a very short time, but if you are feeding the tool with 50’ of 3/8 hose you’ll have trouble. That cutoff tool you bought is a huge air hog and with that 3/8” hose you just can’t keep it up to speed.
There are solutions. When you buy an air tool ask for the full working load cfm. If they can’t or won’t tell you, don’t buy it. All reputable air tool builders will provide these numbers. If you buy an air tool that uses a lot of air, buy a bigger hose. If the tool comes with a 3/8 npt inlet, don’t drop down to a 1/4” npt on a 3/8” hose. Move up to a 3/8” fitting on a1/2” hose. Don’t worry that the threaded end is smaller than the hose. The friction loss through the fitting is inconsequential. The big concern is friction loss over the length of the hose.
Another option is to buy a different, lower cfm tool that will do the same job. Instead of buying that cutoff tool, buy a pneumatic reciprocating saw. It will use less air and you will find many uses for it. If you must have a rotary cutoff tool buy a 4 1/2” electric angle grinder.
Now on to the air tools that I use most often in my home shop:
1. Angle die grinder. This tool gets use at least once a week or more. Once you discover all of the different roloc discs, you will love this tool
2. Angle die grinder – Did I mention that I love this tool.
3. 3/8” stubby air ratchet.
4. 3/8” air drill.
5. Recip saw.
6. 1/2" impact wrench.
7. Orbital sander.
8. Palm sander.
9. Long board.
10. Sandblaster.
11. Straight die grinder.
12. Cutoff tool ( I almost always grab the electric first).
13. Jitterbug (I picked up a pair of them for $5 at a yard sale, but I almost never use them).
One more thing… Please put a drop or 2 of oil in the inlet before each use of any air tool.
Oh btw I run all of these tools with a Campbell Housefeld 6.5 cfm compressor that I bought in 1983. I am waiting for this compressor to die. I just can’t convince the wife that a bigger compressor would make me a more loving husband. When I need more air (sandblasting) I tee in a 5.7 cfm Eagle portable that I pickuped a couple of years ago to power a nail gun. |
|
Back to top |
|
 |
DaveTrig Samba Member
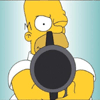
Joined: May 12, 2008 Posts: 166 Location: Mahopac, NY
|
Posted: Wed Sep 24, 2008 9:29 am Post subject: |
|
|
zxylon wrote: |
Should I just run straight power to a new box just for the compressor? |
If by 'straight power' you mean tapping from the main to a subpanel, the answer is NO. Under no circumstances should you ever do a direct tap from the main feed.
The proper thing to do is connect a subpanel to an appropriate double breaker in the main panel. If your existing panel is full, then just bring a couple of circuits from the main panel to the subpanel to make room. So if you want to install a 100 amp subpanel, put a 100 amp 220v breaker in the main panel, and run 3ga wire to your subpanel. Also note that the ground and neutral in the subpanel are left unbonded.
Lemme know if you have any other questions. _________________ DaveTrig
'72 Ghia Convertible
'71 SuperBeetle Convertible
=  |
|
Back to top |
|
 |
AJ Quick Samba Member
Joined: July 20, 2006 Posts: 539 Location: Minnetonka, MN
|
|
Back to top |
|
 |
ArnoudH Samba Member
Joined: December 30, 2008 Posts: 162 Location: The Lowlands
|
Posted: Sun Feb 08, 2009 12:55 pm Post subject: |
|
|
Hi!
What is mostly forgotten es that the majority of compressors intended for the home market(DIY kind of activities) are not built for continueus use.They need a certain time to cool off-especially when they are not force-cooled.Someone mentioned that industrial quality compressors use cast-iron cilinders-that is not true.It's actually the other way around,nowadays(well for a long time now)crome or ceramic-coated liners are used in aluminium cilinders(better heat transfer).
For something different-how do you get rid of the water(or moisture)in your air?Moisture trap-air dryer?
Greets,Arnoud |
|
Back to top |
|
 |
ocbugger Samba Member
Joined: April 24, 2008 Posts: 96 Location: Orange County
|
Posted: Mon Feb 09, 2009 9:48 am Post subject: |
|
|
I have an after cooler mounted on the compressor that lowers the air temp so that it is close to ambiant air temp. It is pretty simple looking, a small unit with air fins. It is not an air dryer but it does cool the air before it leaves the compressor. I then piped out with 3/4" about 40' to the first airline and have a general purpose air/moisture filter with regulator for general air tool use. I then have another airline about 20' from that with a multi-stage filter that I use only for spraying. The multi stage filter removes the smaller contaminants down to .01 micron. Also, at each drop I installed a drip leg. No problems at all. |
|
Back to top |
|
 |
blacktruck Samba Member
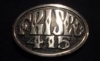
Joined: September 23, 2005 Posts: 377
|
Posted: Mon Apr 06, 2009 1:18 pm Post subject: |
|
|
does someone have a link or a how to on making a compressor out
of a vw engine?seems like a cool project.good way to utilize parts
that might not get used(009,single relief case etc.) |
|
Back to top |
|
 |
xLINKx Samba Member
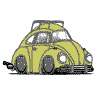
Joined: August 28, 2008 Posts: 2 Location: Santa Cruz
|
Posted: Mon May 04, 2009 11:32 am Post subject: paint and body compressors |
|
|
For your compressor needs one must add up the cfm or scfm of the tools being used with the compressor at the same time. Then get a compressor that will exceed that need. Only then will one have a good compressor. I have seen some compressors that have a 10 gal tank but only a 2.5 cfm @ 90 psi. This is only good for bike tires and rubber balls.
CHECK the INTERNET for the formula.  |
|
Back to top |
|
 |
Matty8251 Samba Member
Joined: May 30, 2009 Posts: 8 Location: Middleburg, FL
|
Posted: Wed Jun 03, 2009 7:25 pm Post subject: commpresser |
|
|
I use a 6.5hp 60gal and it works great. If you are using a HPLV paint gun you will have no problem with at size. If you are using a DA sander it will run a lot, but will do the job with no problem if you dont mind the noise of the commpresser running. Also if you are painting please get a drier if you can, it will also help save your other airtools. |
|
Back to top |
|
 |
weux Samba Member
Joined: June 25, 2008 Posts: 57 Location: St Louis Park, MN
|
Posted: Tue Jun 23, 2009 8:12 pm Post subject: |
|
|
blacktruck wrote: |
does someone have a link or a how to on making a compressor out
of a vw engine?seems like a cool project.good way to utilize parts
that might not get used(009,single relief case etc.) |
http://www.dunnrightinc.com/ _________________ 1970 Standard Beetle |
|
Back to top |
|
 |
|